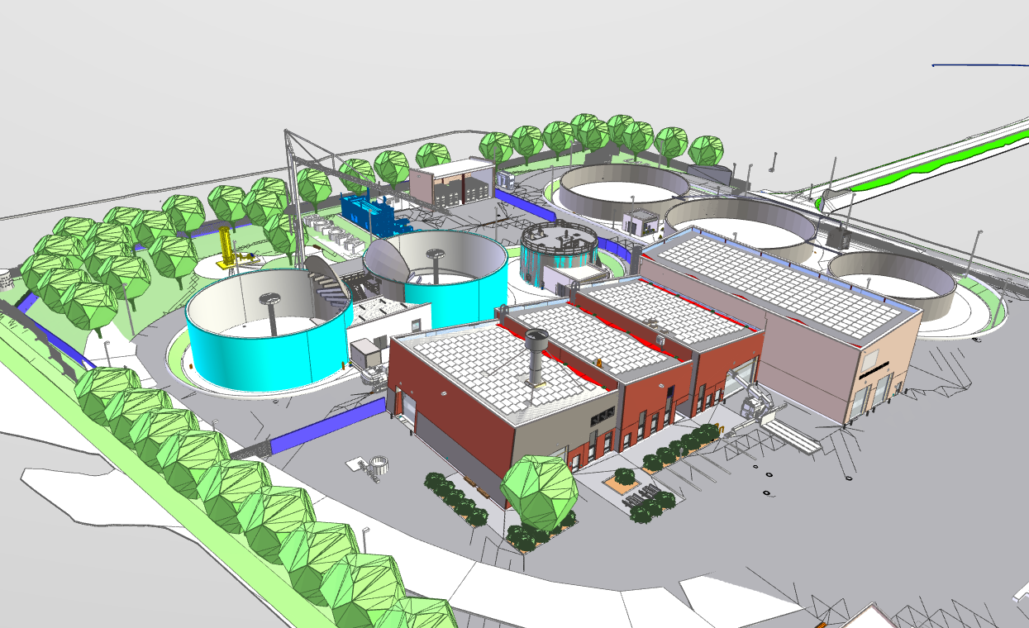
In this article, we take a sneak peek behind the scenes of Voss biomethane plant construction.
As you may know, Biovoima’s main working principle is to be a technology integrator. This means that the key to our customer’s success lies within the equipment that we choose for different process steps: what, why, and how they work together. Decisions are always made project-by-project based on the customer’s project budget and the performance values that want to be or need to be reached at the plant. Biovoima is typically in a role of EPC-contractor, having full responsibility of the total engineering, procurement and construction.
In Voss plant, end customer being BIR AS, the biggest waste handling company of Bergen region in Norway, these demands were specified in a public tender.
Let’s dive into the process steps, shall we?
Waste reception
BIR delivers the organic household, restaurant and grocery store waste to the biomethane plant with packer trucks and inside containers. Also liquid manure is received with tanker trucks directly from local farms. To avoid odors to spread and establish more convenient working environment for the drivers, all waste reception happens indoors.
As being in an arctic atmosphere during the wintertime, it is utmost important that the reception silos are solid and robust enough to endure dipping of (more or less) frozen waste transportations. Also seamless interaction between reception and pre-treatment equipment is important to enable stable feeding to the pre-treatment system and biogas process, respectively.
This is why the whole downstream equipment set has been ordered from Mavitec Green Energy, a close partner of Biovoima: they have a wide experience of both receiving and pre-treating the waste. This way we can trust that no frustrating bottle necks are formed in the front-end of the waste process.
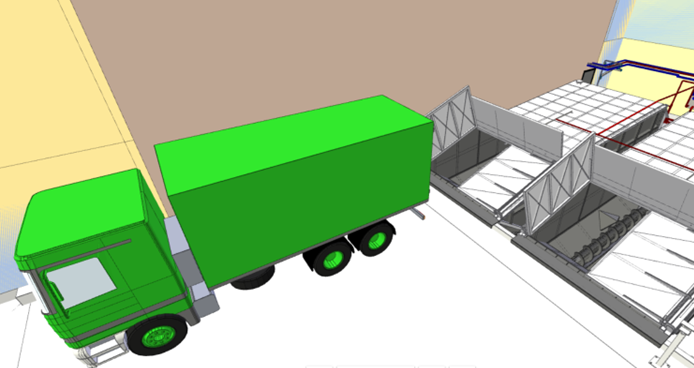
with 2x waste dipping silos
Waste pre-treatment
As mentioned regarding waste reception, Mavitec technology handles also the pre-treatment of the waste. In practice this means separating the organic fraction from the packaging materials and establishing the maximum allowed particle size for pasteurization. Pre-treatment is done with a paddle depacker i.e. paddle mill, which is one of the very best equipment when your goal is to:
- use as little dilution water as possible, but still
- reach enough high purity of the organic stream, for that digestate coming out from the biogas process will reach the maximum allowed impurity % of European organic fertilizer laws without any further treatment.
After the pre-treatment process, organic pulp is pumped into a buffer tank where it is mixed with slurry. After mixing, the feedstock stream for the biogas process is ready. Packaging material will be collected as high-quality RDF (refuse-derived fuel) into transportation containers and sent to BIR’s incineration plant for further energy production.
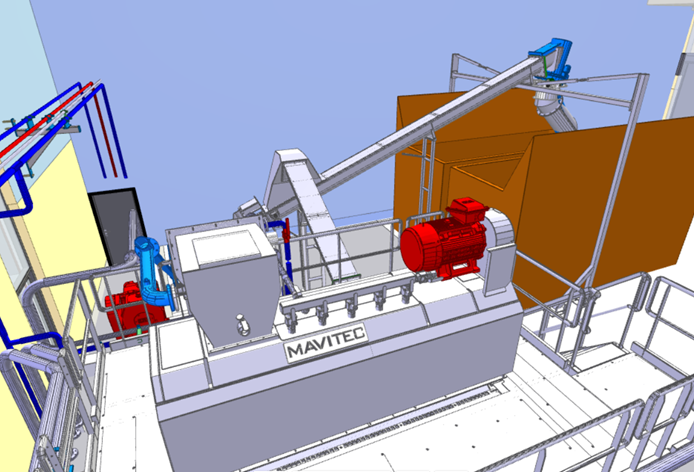
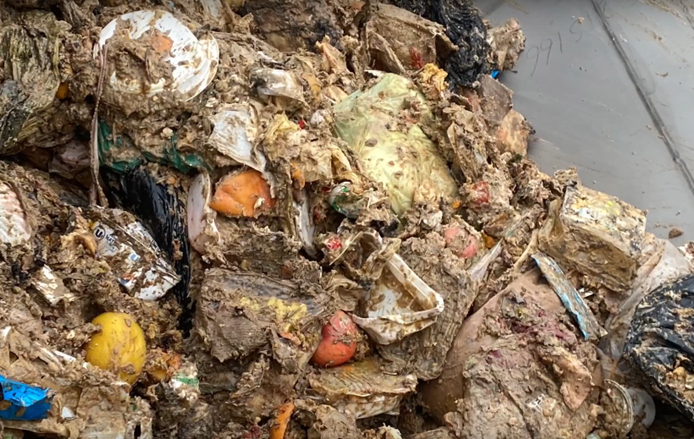
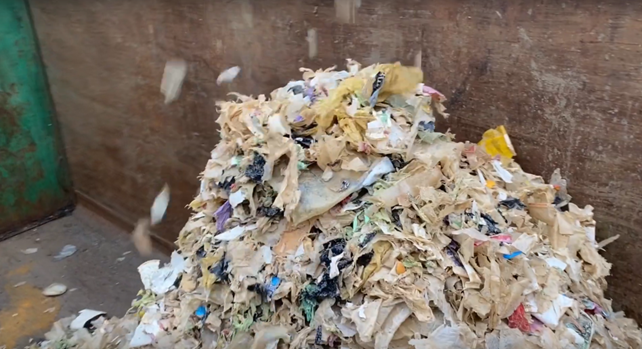
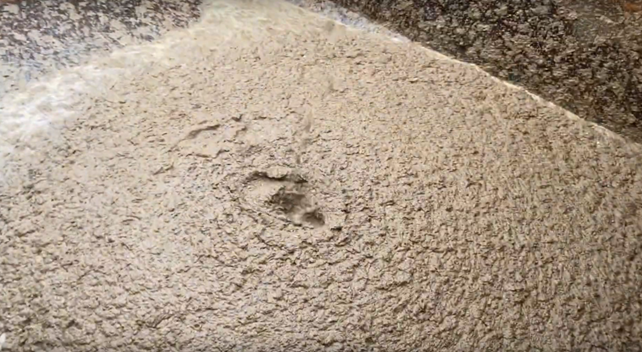
Pasteurization and heat recovery
Pasteurization is an EU-required process where the organic material is heated up to 70 °C for one hour to kill salmonella and other pathogens that could potentially cause health issues when using the digestate as fertilizer. Pasteurization solution in Voss plant is Biovoima’s own product, BIOpasteurizer using so called “continuous batch process”, where one batch is always in preparation for an hour retention, the second is being kept in 70 °C for one hour, and the third is being emptied. In continuous operation like this, the heat recovery is optimal.
In practice, pasteurization is a complex of tanks, pumps, pipes, valves and heat exchangers. Even 70 % of the used heating energy can be recovered with proper technical solutions. We even recover heat in two stages: first the incoming material is pre-heated with output from the digesters (~40 °C), after which the pre-heating is continued with output from the previous pasteurization batch (~70 °C). This way a high temperature will be reached for the material to be pasteurized, even before any heating! This will be achieved with unique direct sludge-to-sludge heat exchangers by Westcome Heat Exchangers.
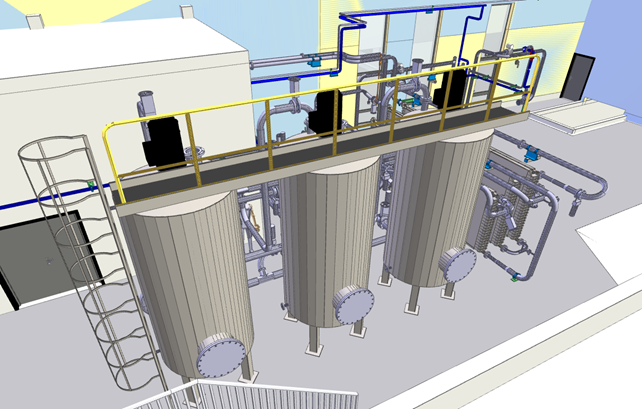
Odor control
Because the biogas plant is located close to private housing area, the odor gases generated in waste storage and processing need to be carefully purified before discharge to the atmospere. In this area, the technology by Scandinavian Centriair AB comes into the picture. All major odor sources are equipped with point collection system, and this highly concentrated air will be treated with different technologies, selective for the particular odor gases forming in each source. Before releasing to the athosphere, combination of activated carbon and UV-reactors will take care of destroying the remaining odor components.
Biogas process
In the Voss biomethane plant, biogas production will happen inside the biogas digesters by Kanadevia Inova, using Schmack Biogas digester technology. Uniqueness of Schmack technology comes from the giant Remex agitators. These slow-rotating paddle agitators need very little electricity to operate yet making it possible to have higher solid material concentration inside the digesters than in traditional wet fermentation digesters (or so called CSTR reactors). This further enables the plant operation with lower heat consumption, because there is less water to heat up to process temperature, being typically around 40 °C.
Another uniqueness of Schmack digester technology is the wooden “false ceiling” structure, which will form a microfilm surface for H2S removal. Consequently, about 50 % of formed H2S will be removed already inside the digester, which makes the investment to additional H2S removal technologies (activated carbon, scrubber, etc.) smaller – especially maintenance wise.
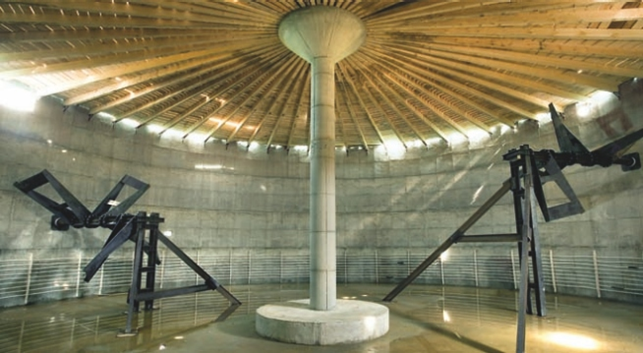
Biofertilizer
After the organic matter of the waste has turned into biogas, wet and highly nutritious sludge remains. This sludge is called digestate, an organic fertilizer. Digestate has the same nutrients as the material that it is made of (in this case, 1/3 food waste and 2/3 cow slurry), but in hygienic and more soluble (=better) form.
In Voss project, biofertilizer will be (as it often is) separated into solid and liquid fractions. However, the specialty for the equipment selection came from the demands of local farmers. In Voss area, it is important to strictly control the amount of phosphorus being spread on the fields. Therefore, the separation technology had to be selected according to the best phosphorus separation efficiency.
A decanter centrifuge by Alfa Laval will power up the separation process. With centrifuge, a higher separation efficiency for phosphorus (to the solid fraction) and nitrogen (to the liquid fraction) will be received than for example with screw press separators. Consequently, farmers can easily adjust the nutrients that will be spread on the fields, without worry of over fertilizing.
Biogas upgrading
The biogas that forms in the biogas digesters will be further refined into biomethane, i.e., purified from CO2 and other gas components. This happens in biogas upgrading system.
For biogas upgrading, several different technical solutions exist. Four main technologies are water scrubbing, amine scrubbing, membrane and PSA (Pressure Swing Adsorption). Water scrubber is an affordable solution, which however comes with some risks for biomethane quality, especially in cold atmospheres. Amine scrubber on the other hand is the best solution when lots of excessive heat is available but can become costly in projects without it. In addition, tender required us to use as little water and chemicals as possible. This left PSA and membrane in the final evaluation.
Even though Biovoima has its own membrane-based biogas upgrading technology BIOupgradeCH4, a PSA-system by Provedal was introduced into the Voss project. This is because membrane, currently the most popular biogas upgrading technology in the world, has a very appealing investment cost but higher electricity consumption. The bigger the biogas flow gets, the faster the gap in the investment cost caught up by lower operation cost of PSA system (lower electricity consumption and lower maintenance cost). In Voss project, because lifecycle cost is the most important, this scale turned towards PSA. Both can produce similarly high-quality end product, biomethane.
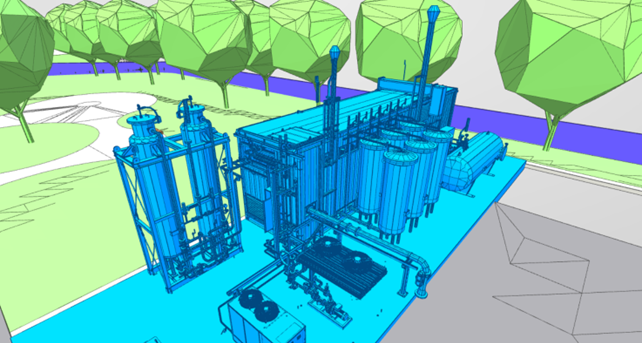
Gas pressurization
After biomethane has been produced, a typical final step is injection into the natural gas grid to replace fossil gas with similar properties. However, in Voss area, there is no natural gas grid. Therefore, the gas needs to be compressed into as small volume as possible – either to establish efficient transportation to industrial users inside gas transportation containers, or to power up BIR’s own waste collection trucks.
Supplier of this high-pressure (250 bar) methane compressor, Italian Fornovo Gas, is a market leader with more than 2,500 compressor installations. Fornovo Gas is also a long-time partner for Biovoima.
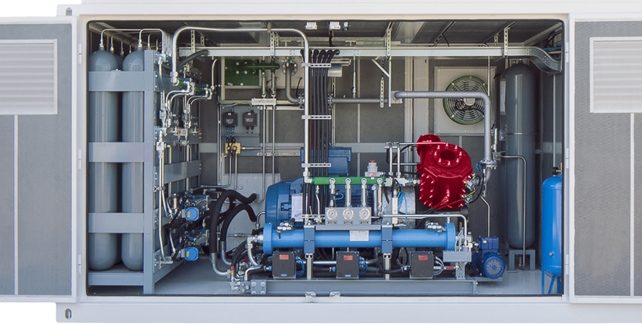
Gas filling station
As mentioned above, produced biomethane will be used as 100 % renewable fuel both in industry and in BIR’s and its partners’ waste collection trucks. Logistics of the gas for industrial users will happen with high-pressure gas transportation containers. The plant’s automation will take care of the tracking of gas amount being filled into each container, so that BIR can easily arrange the logistics and invoicing. The same applies to the trucks with Biovoima´s gas filling station on the plant, BIOpark: for the driver, the process is similar to refueling the truck (or a private car) at a regular gas station. Price will be automatically adjusted according to the agreements between BIR and the companies filling their trucks with compressed biomethane, or more regularly CBG (compressed biogas) which is chemically similar to CNG (compressed natural gas), but in renewable ecofriendly form.
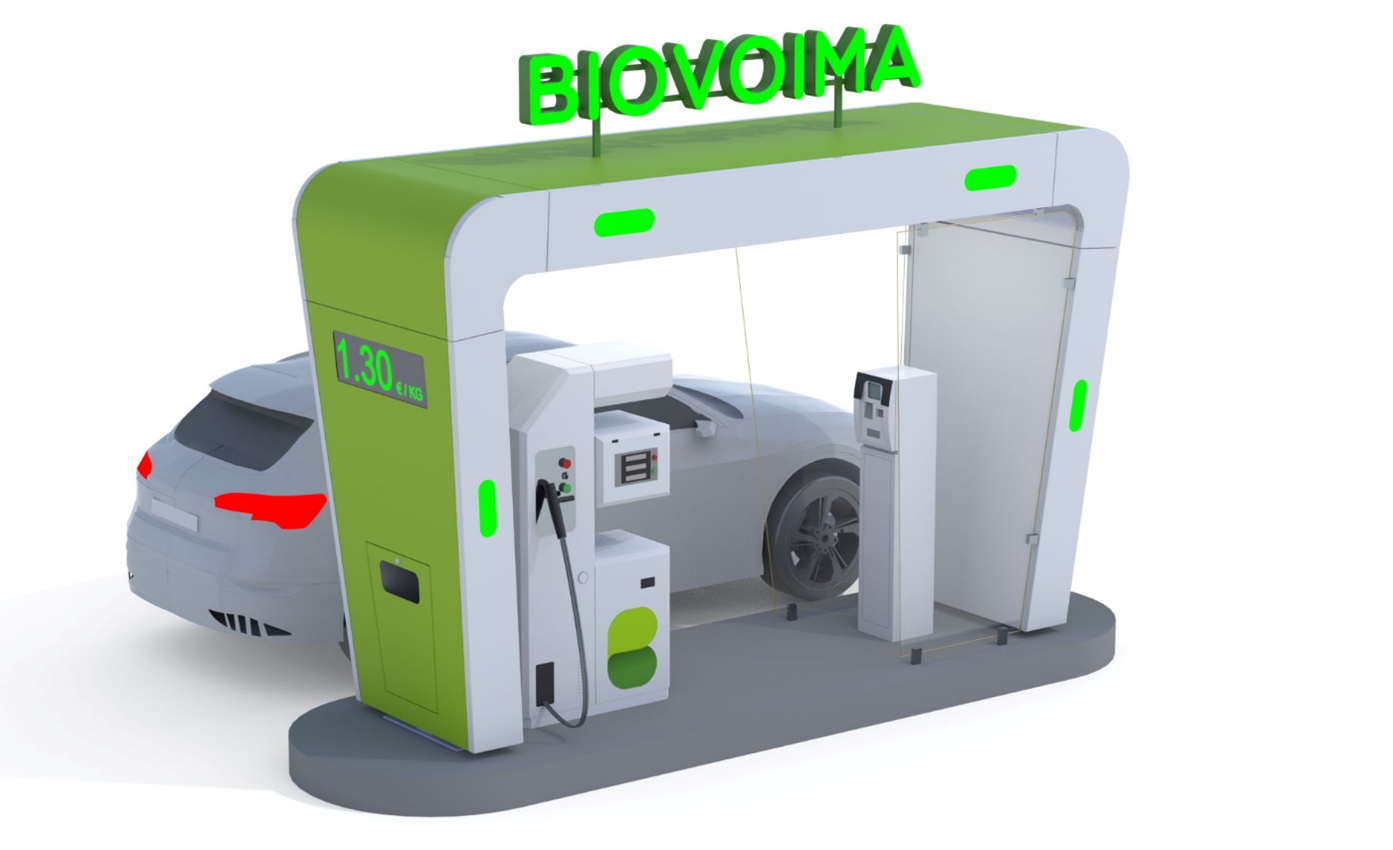
Automation
To ensure seamless operation between several different equipment entities, requirements are high for the automation system. Having experience from some of the most complex biorefineries of the whole world, Valmet Automation was chosen to provide “an umbrella” above the whole Voss biogas plant as well. High user-friendliness combines with Finnish quality, outstanding security and easy integration of different sybsystems were the main selection criteria for Valmet.
Summary and general information
The biogas plant in Voss is the first of its kind in Vestland Norway and will produce biogas from collected food waste from the region and local manure from farmers. Processing capacity is total of 54,000 tons of organic streams per year. Most of the biofertilizer produced in this process will replace the use of cow manure as fertilizer, and along with this, methane emissions and odors from agriculture are significantly reduced. Because of better fertilizer features than manure, this may also reduce the import of fertilizers.
The biomethane produced at the plant will be used as fuel primarily for BIR’s heavy vehicles, in addition to environment friendly alternative for fossil natural gas / LNG in the industrial sector in and around Voss area. In order to be able to use the biogas locally, processes are underway to establish also a filling station in downtown Voss. The vehicles will literally be powered by local food waste and cow manure – a great example of good application and circular value chains in practice.
Biovoima is proud and glad to be a part of the chain for bringing this all into life!
More information about the project:
Jani Kangasaho
Sales Director, Partner
Tero Kemppi
Project manager
+358 50 408 7100